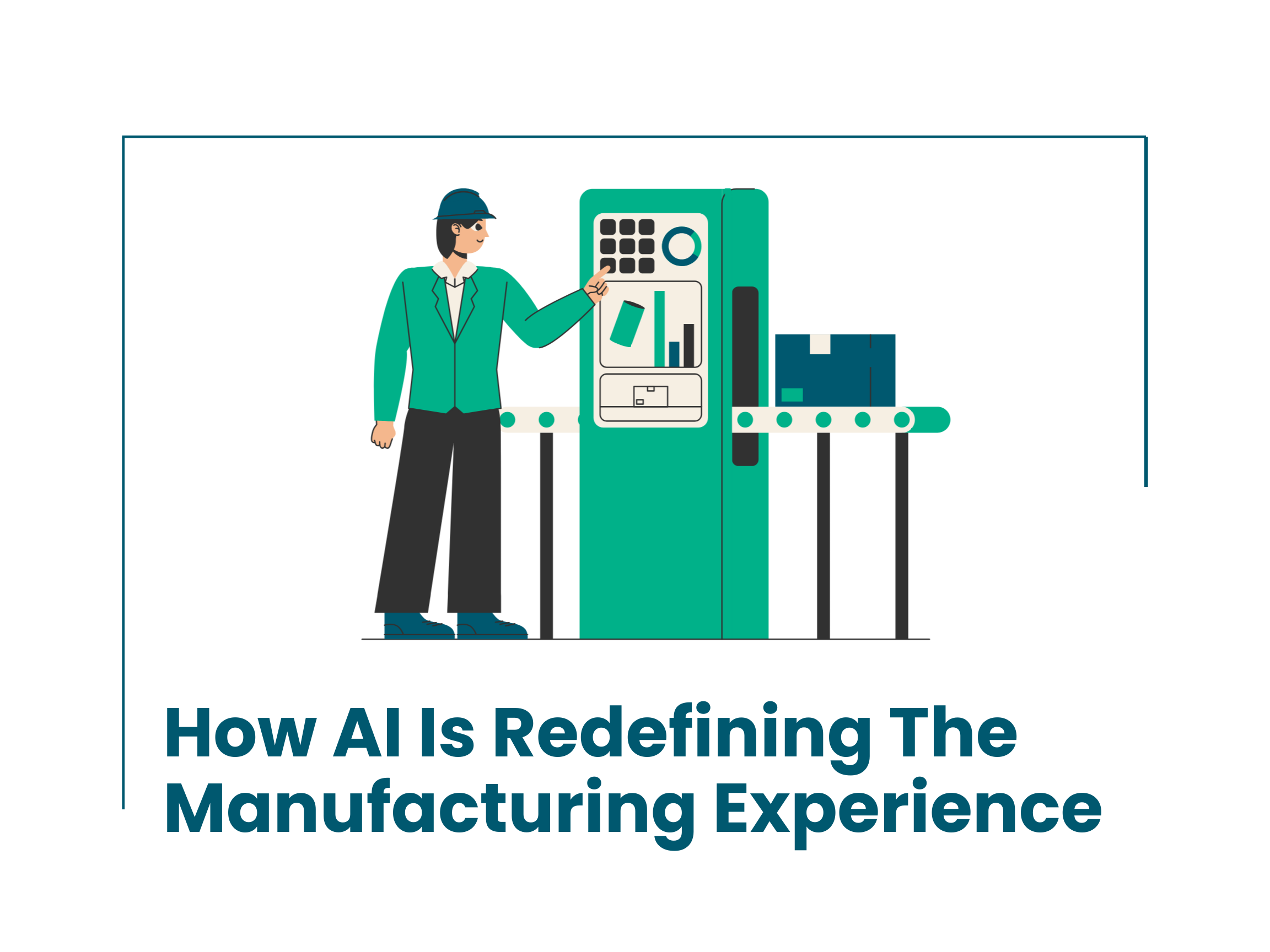
Contents
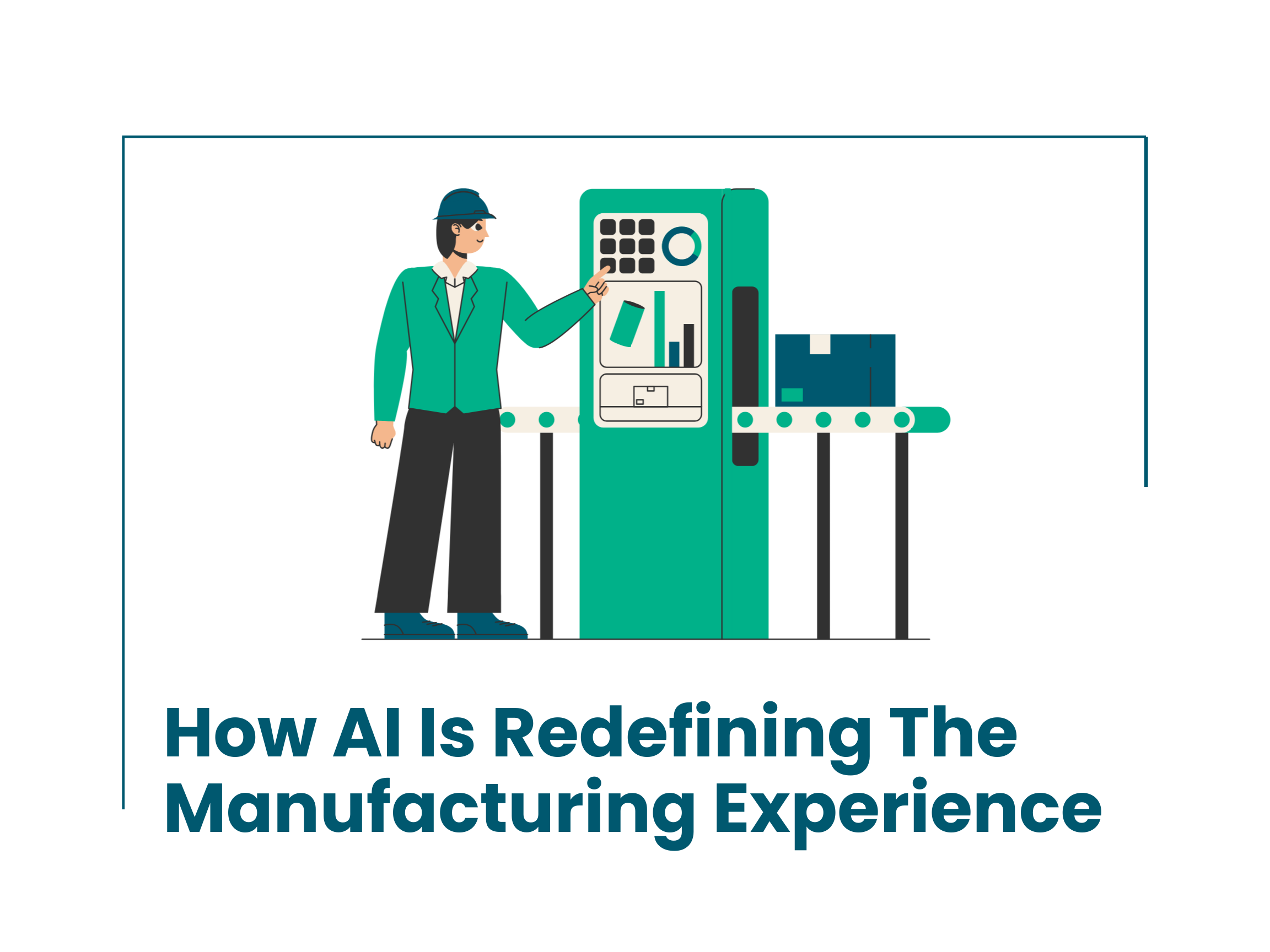
Manufacturing, an industry often plagued by inefficiencies and operational challenges, is experiencing a significant transformation through the integration of Artificial Intelligence (AI). Traditionally viewed as a domain of heavy machinery and manual labor, manufacturing is now at the forefront of technological innovation.
AI's integration into manufacturing processes promises enhanced efficiency, improved safety, and substantial cost savings. Traditional pain points that have long hindered productivity, safety, and cost-effectiveness are now being effectively tackled with advanced AI tools.
What does this mean for decision-makers as they lead their companies in modern, high-tech manufacturing? In this article, we explore the critical challenges and examine how AI is reshaping the landscape. We provide insights into AI's applications in enhancing safety, enabling predictive maintenance, improving quality control, optimizing processes, and refining intelligent demand forecasting.
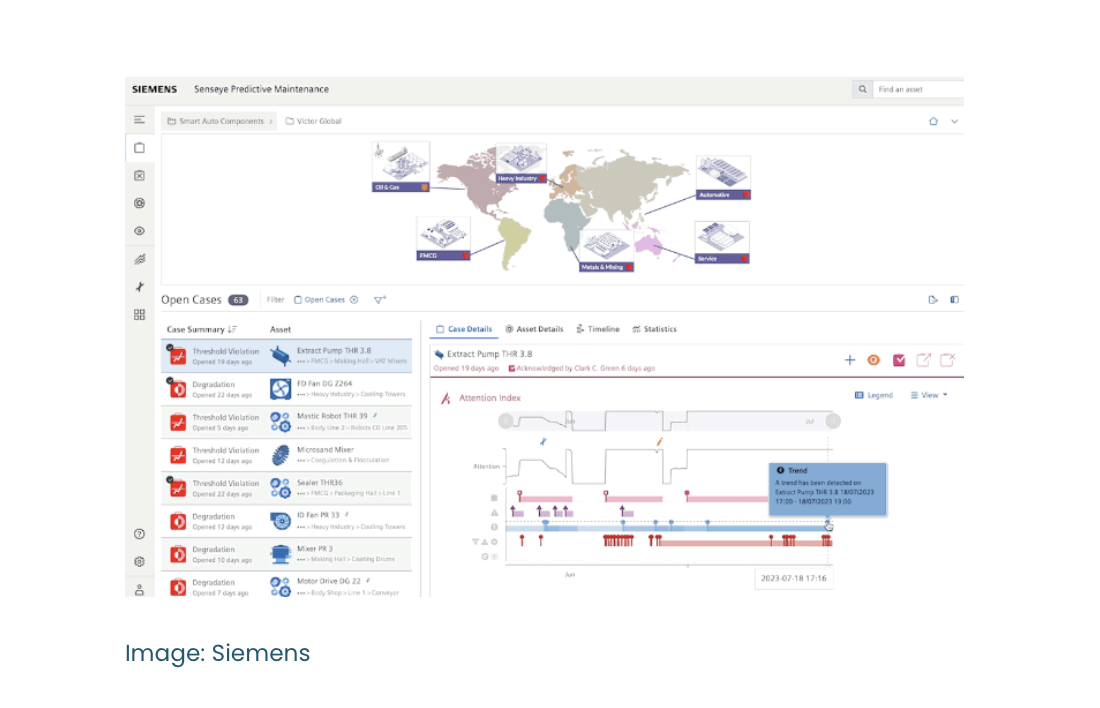
Predictive Maintenance
One of the most significant challenges in manufacturing is dealing with unexpected equipment failures, which will cause costly downtimes and disrupt production. Traditional maintenance practices, often based on fixed schedules, can either be too frequent, wasting resources, or too late, leading to unplanned stoppages.
To tackle these challenges head-on, enterprises have turned to predictive maintenance as a proactive strategy to equipment maintenance. AI-driven predictive maintenance offers an optimized solution by leveraging advanced machine learning algorithms and IoT data. These technologies continuously monitor the condition of machinery, analyzing data such as vibration, temperature, and energy consumption to predict the machine’s health and performance. Leveraging real-time data and advanced analytics enhances safety and ensures that maintenance is conducted only when necessary.
For instance, General Electric (GE) uses AI to predict maintenance needs for its jet engines, significantly reducing unscheduled maintenance and operational disruptions. Similarly, BlueScope is utilizing Siemens’ new generative AI functionality in Senseye Predictive Maintenance, to scale knowledge across global teams. By implementing predictive maintenance, manufacturers can not only enhance equipment reliability and extend its lifespan but also achieve substantial cost savings and improve overall operational efficiency.
There are many AI tools available to assist with predictive maintenance. However, a comprehensive AI System Selection engagement is highly recommended before committing to a specific AI solution. This ensures that the chosen AI tool aligns perfectly with the specific needs and operational goals of the organization, maximizing its effectiveness and return on investment.
Improving Quality Control
Quality control is a critical aspect of manufacturing, as even minor defects can lead to significant financial losses and damage to a company's reputation. Traditional quality control methods, which rely heavily on manual inspections, are often slow and prone to human error, resulting in missed defects and inconsistent product quality. AI is transforming this landscape by introducing advanced machine learning algorithms and computer vision technologies. These AI systems can analyze images and data from production lines in real-time, identifying defects with far greater accuracy and speed than human inspectors.
For example, companies like Bosch are introducing AI-powered visual inspection systems to detect anomalies in product components, ensuring that only high-quality parts proceed to assembly. Similarly, Intel employs AI to inspect semiconductor wafers, drastically reducing the incidence of faulty chips.
By automating quality control processes, AI not only enhances product quality but also increases efficiency, reduces waste, and lowers production costs. This technological advancement allows manufacturers to maintain stringent quality standards while meeting the demands of high-volume production.
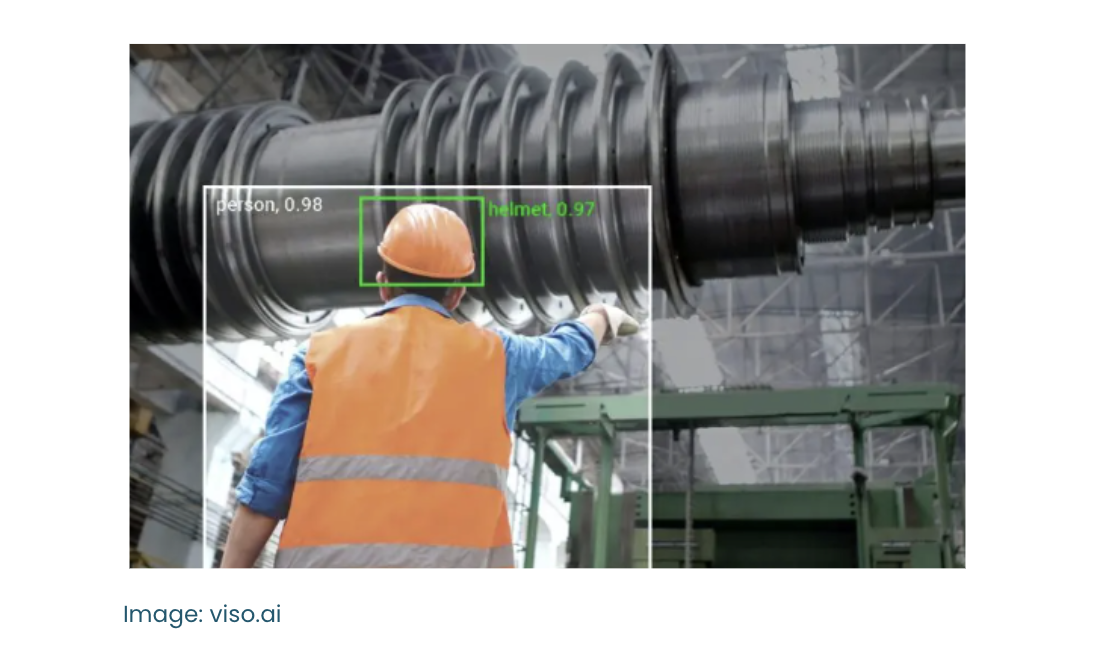
Optimizing Processes
Optimizing manufacturing processes is essential for enhancing efficiency, reducing costs, and staying competitive in the market. However, traditional methods of process optimization are often manual, time-consuming, and based on limited data, making it challenging to identify bottlenecks and inefficiencies.
AI is revolutionizing process optimization by leveraging advanced analytics and machine learning algorithms to analyze vast amounts of data from various stages of production. These AI systems can identify patterns and trends that humans might overlook, providing actionable insights for improving workflows.
For instance, at Procter & Gamble, AI-driven analytics are used to streamline production lines for products like diapers and paper towels, ensuring that resources are utilized efficiently and production schedules are met. AI can also predict demand fluctuations, allowing manufacturers to adjust production rates dynamically to avoid overproduction or underproduction.
This level of optimization helps companies achieve higher productivity, lower operational costs, and a more agile response to market changes. By integrating AI into their operations, manufacturers can continuously improve their processes, leading to sustainable growth and a competitive edge in the industry.
Intelligent Demand Forecasting
Accurate demand forecasting is crucial for manufacturers to manage inventory, plan production schedules, and meet customer expectations. Traditional demand forecasting methods often struggle with processing large datasets and fail to capture complex market dynamics, leading to issues like overproduction, stockouts, and increased holding costs.
AI-driven demand forecasting offers a transformative solution by leveraging machine learning algorithms and big data analytics to predict future demand with high accuracy. These AI systems analyze vast amounts of data, including historical sales, market trends, and external factors such as economic indicators and seasonal variations.
For example, Coca-Cola uses AI to forecast demand across its extensive product range, ensuring optimal inventory levels and reducing waste. Similarly, Unilever employs AI to predict demand for its consumer goods, adjusting production schedules and supply chain logistics to match real-time market needs. AI can also respond dynamically to unexpected changes in demand, such as sudden spikes during promotional events or shifts in consumer preferences. By integrating AI into demand forecasting, manufacturers can improve their agility, reduce costs associated with excess inventory, and enhance customer satisfaction by ensuring product availability. This advanced approach to demand forecasting enables manufacturers to stay competitive and responsive in a rapidly changing market landscape
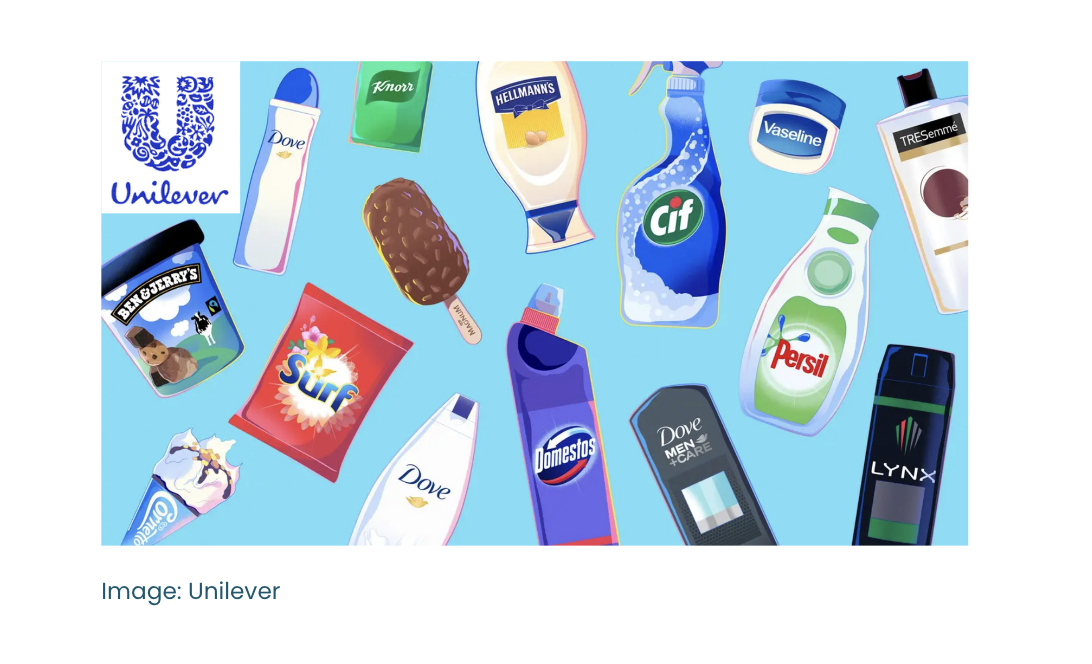
Integrating AI into manufacturing is not just a technological upgrade but a paradigm shift redefining the industry. As manufacturers embrace AI, operations become safer, more efficient, and responsive to market demands. Staying at the forefront of AI advancements secures a competitive edge and paves the way for sustainable growth.
At Louder Co., we offer a holistic approach to AI, ensuring that your business not only adopts AI but thrives with it. If you're ready to get started on your AI journey, get in touch today! Together, we can turn the complexities of AI into opportunities for growth and success.